Important: The Groundsmaster 360 must be equipped with the Electrical Accessory Kit, Part 115-0019, to operate the Quick Attach Front Frame Kit.
Toro Groundsmaster 300, 325D, 327, 328D, 332D and 345 Mower Parts Quick Reference Guides. Find Air filters, oil filters, spark plugs and more for your Toro mower fast with these guides. Toro groundsmaster 325 d. Mitsubishi K3D Diesel Engine Toro Groundsmaster 325D RARE! TORO GROUNDSMASTER PARTS 322D 325D 328D 345 MOWER GROUNDS MASTER TORO. $15.00 shipping. TORO GROUNDSMASTER MOWER PARTS CONTROL PANEL WIRING HARNESS 322 325D 328D. Hi All I just got a nice Toro Groundsmaster 325D in good shape with a Cozy Cab and a Toro 150 snow thrower. The challenge is that I don't have the 'Quick Attachment Kit' to make the connection from the arms to the thrower. Just bought a 325-D 4WD With 2,500hrs and the Guardian Recycler 72' deck. Now begins the desperate search for the 2760 Flail Mower attachment. Any toro groundsmaster fans on here? Parts that fit the Toro Groundsmaster 328D. The different products for your Groundsmaster 328D are easily found in the parts manual. If you don't have these documents, our parts specialist can help you to find the right parts for your machine. On our website you will find a clear overview of the products that are available for your Toro rotary.
This product complies with all relevant European directives. For details, please see the Declaration of Incorporation (DOI) at the back of this publication.
Safety decals and instructions are easily visible to the operator and are located near any area of potential danger. Replace any decal that is damaged or missing. |
133-8061
Park machine on a level surface with the cutting deck in the fully raised position. Shut off the engine, engage the parking brake and remove the key.
Note: When the cutting deck is in the raised position, the pull link torsion spring tension is reduced making it much easier to disconnect the pull links from the machine.
Disconnect the pull link from each side of the machine as follows:
Be careful when disconnecting the pull links. The pull link torsion springs may cause some rotation of pull links during the removal process.
Remove the shoulder screw that secures the retainer pin to the carrier frame (Figure 1).
Figure 1
- Shoulder screw
- Retainer pin
- Ring pins and clevis pins
Carefully slide the retainer pin from carrier frame and the pull link.
Note the location of the height-of-cut pin in the height-of-cut bracket for re-assembly purposes (Figure 2). Remove the height-of-cut pin from the height-of-cut bracket.
Figure 2
- Height-of-cut pin
Position suitable furniture dollies under the cutting deck.
Start the engine and fully lower the cutting deck onto the furniture dollies. Shut off the engine and remove the key from the ignition switch.
Do not start the engine and engage the PTO switch when the PTO shaft is disconnected from the cutting deck. If the engine is started and the PTO shaft is allowed to rotate, serious personal injury and machine damage could result. Remove the PTO fuse from fuse block to prevent unintentional engagement of the PTO clutch.
Lift the floor plate, exposing the top of the cutting deck.
Disconnect the end yoke of the PTO shaft from cutting deck gearbox shaft as follows.
Remove the roll pin from the end yoke and the gearbox shaft (Figure 3). Retain the roll pin for re-use.
Figure 3
- Gearbox
- PTO shaft end yoke
Loosen the 2 capscrews and locknuts (Figure 3).
Slide the driveshaft end yoke from gearbox shaft and tie them up to the frame for support.
Remove the 4 ring pins and clevis pins that secure the deck lift chains to the adjustment clevises on the cutting deck (Figure 1).
Roll the cutting deck away from the machine.
Toro Groundsmaster 325d Deck Parts

Mounting the Hydraulic Tubes to the Front Attachment Frame
Parts needed for this procedure:
Front attachment frame | 1 |
Hydraulic tube, shorter | 1 |
Hydraulic tube, longer | 1 |
Loosely install the shorter hydraulic tube to the straight fitting on the valve (Figure 4).
Loosely install the longer hydraulic tube to the straight fitting on the manifold (Figure 4).
Figure 4
- Shorter hydraulic tube
- Valve
- Longer hydraulic tube
- Manifold
Parts needed for this procedure:
Screw (1/2 x 1-1/4 inches) | 4 |
Flange nut (1/2 inch) | 11 |
Screw (1/2 x 4-1/2 inches) | 6 |
Spacer | 4 |
Screw (1/2 x 3-1/4 inch) | 1 |
Support washer | 2 |
Spacer | 1 |
Figure 5 shows the top view of the location, positioning, and size of the fasteners used to secure the front attachment frame to the underside of the traction unit frame.
Figure 5
- Front attachment frame
- Screw (1/2 x 1-1/4 inches) and flange nut (1/2 inch)
- Screw (1/2 x 4-1/2 inches)
- Spacer
- Screw (1/2 x 3–1/4 inches), support washers, and locknut (1/2 inch)
- Lock pin
- Hair pin cotter
Guide the shorter hydraulic tube assembly (Figure 4) around and above the traction control rod.
Position the front attachment frame under the front of the machine (Figure 6).
Raise the front attachment frame while aligning the mounting holes with the mounting holes in the frame channels and the front frame cross plate (Figure 6).
Figure 6
- Screw (1/2 x 1-1/4 inches) and flange nut (1/2 inch)
- Screw (1/2 x 4-1/2 inches) and flange nut (1/2 inch)
- Screw (1/2 x 4-1/2 inches), spacer, and flange nut (1/2 inch)
- Screw (1/2 x 3-1/4 inches), support washers, and locknut (1/2 inch)
On the front of the attachment, secure the outer hole, on each side, to the frame channels with a screw (1/2 x 4-1/2 inches) and a flange nut (1/2 inch) as shown inFigure 6.
On the rear of the attachment, loosely install each side to the frame channels with 2 screws (1/2 x 1-1/4 inches) and flange nuts (1/2 inch) as shown inFigure 6.
Using the remaining 4 mounting holes, secure the attachment to the frame cross plate with screws (1/2 x 4-1/2 inches), spacers, and flange nuts (1/2 inch) as shown inFigure 6). Position the spacers between the screw head and the cross plate.
Tighten the fasteners to 91 to 113 N⋅m (67 to 83 ft-lb).
Secure the top link assembly to the axle support with a screw (1/2 x 3-1/4 inches), 2 support washers, spacer, and a locknut (1/2 inch) as shown in Figure 5 and Figure 6.
Note: The washers are to be positioned on the outside of the ears on the axle support. Figure 7).
Figure 7
- Locknut (1/2 inch)
- Spacer
- Support washer
- Screw (1/2 x 3-1/4 inches)
Torque the screw to 91 to 113 N⋅m (67 to 83 ft-lb).
Parts needed for this procedure:
Tube clamp | 1 |
Plate | 1 |
Tube clamp | 1 |
Plate | 1 |
Carriage screw | 2 |
Flange nut | 2 |
Place a drain pan under the caps on the hydraulic tubes (Figure 8).
Remove the caps from the hydraulic tubes on the machine (Figure 8). Remove the caps one at a time as installing the tubes to prevent excess hydraulic fluid loss.
Figure 8
- Hydraulic tube caps
Connect the rear end of the shorter hydraulic tube to the tube on the machine (Figure 9).
Figure 9
- Shorter hydraulic tube
- Valve
- Longer hydraulic tube
- Manifold
- Tube clamp, small
- Tube clamp, large
- Plate, small
- Plate, large
Connect the rear end of the longer hydraulic tube to the tube on the machine (Figure 9).
Tighten connections.
Loosely secure the shorter hydraulic tube to the adjacent tube, on the machine, with the smaller tube clamp, plate, carriage screw, and flange nut, as shown in Figure 9.
Loosely secure the longer hydraulic tube to the adjacent tube, on the machine, with the larger tube clamp, plate, carriage screw, and flange nut, as shown in Figure 9.
Tighten the carriage screws and nuts.
While aligning the driveshaft mounting holes with the jack shaft hole, slide the driveshaft onto the attachment jack shaft (Figure 10).
Figure 10
- Driveshaft
- Jack shaft
Secure the driveshaft to the jack shaft with the roll pin previously removed.
Tighten the 2 driveshaft cap screws and locknuts.
Parts needed for this procedure:
Switch | 2 |
Decal | 1 |
Use a knife to cut out the provided decal.
Remove the knock-out by pressing on it from inside the console.
Install the decal between the switch holes.
Figure 11
- Switches.
- Decal
Install the switches by pressing them into the holes.
Connect the wire harness to the switches.
Test the machine to ensure that all controls and parts are working as expected.
Start the engine.
Raise and lower the quick attach front frame to ensure that all functions are working as expected.
Shut off the engine, engage the parking brake, and remove the key from the ignition switch.
Check for any leaks.
Note: If there are any leaks or if the machine is not performing properly, please review and repeat the steps in this manual to ensure that everything is connected properly.
Note: Determine the left and right sides of the machine from the normal operating position.
Please read all safety instructions and symbols in the safety section. Knowing this information could help you or bystanders avoid injury.
Operating on wet grass, ice or slippery steep slopes can cause sliding and loss of control.
Wheels dropping over edges can cause roll overs, which may result in serious injury, death or drowning.
Read and follow the rollover protection instructions and warnings.
To avoid loss of control and possibility of rollover:
Do not operate near drop-offs or near water.
Reduce speed and use extreme caution on slopes.
Avoid sudden turns or rapid speed changes. Always use seat belts
This machine produces sound levels in excess of 85 dBA at the operators ear and can cause hearing loss through extended periods of exposure.
Wear hearing protection when operating this machine.
The use of protective equipment for eyes, ears, feet and head is recommended.
Figure 12
- Warning— wear hearing protection

To operate the front attachment, use the rocker switches as indicated in Figure 13.
Figure 13
- Front attach raise and hold
- Tap to float front attach down. Hold to power down.
- Swing front attachment right
- Swing front attachment left
Important: Do not hold down the power down switch once the attachment has been fully lowered; this can cause significant hydraulic system damage and result in front attachment damage.
Remove the mower deck as shown in Removing the Cutting Deck, then mount the driveshaft as shown in Mounting the Driveshaft.
Important: The driveshaft cannot be mounted to the front attachment with the deck installed, or else the machine will be damaged.
Using non-powered front attachments with the front deck installed could injure someone or damage the machine.
Do not use non-powered front attachments with the front deck installed.
Clean and grease all front attachments.
Remove the driveshaft.
Install the front deck.
Read the Operator's Manual supplied with the attachment before operating.
Ensure that the hydraulic quick couplers are free of any contaminants before connecting.
Keep the output shaft oiled to prevent rust.
Do not operate the PTO with the attachment in the raised position. Noise from the PTO drive line will be evident.
Install the attachment as follows:
Remove any attachment from the machine. Follow attachment supplier's recommendation for safe blocking and storage.
Drive the machine into position behind the attachment adapter. Raise the machine adapter into the attachment adapter.
Secure the adapters together with the attachment pin and hairpin cotter as shown in Figure 14. For more abusive loading a nut and bolt may be substituted.
Figure 14
- Attachment pin
- Cotter pin
- Machine adapter
- Attachment adapter
Removing the deck
On a flat level surface raise deck to highest position.
Place 2 furniture dollies under each end of the deck and lower it so it rests on the dollies.
Remove the bolts (5/16 inch) and remove the pins from the drag-links on each side of the deck.
Remove the four retainer clips and clevis pins from the chains suspending the deck.
Remove the roll pin and loosen the bolts securing the driveshaft to the deck.
Slide the driveshaft off of the deck gearbox and secure it to the frame of the machine with a bungie cord or strap.
The deck can now be rolled out from under the machine.
If preparing the machine for winter work, it would be advisable to remove the deck hanging chains.
Attaching the deck
If the deck chains were removed from the lift arms, reinstall them.
Raise the drag-links on the deck with a pry bar and place a block (6 x 2 x 4 inch) under each one to lift the arm up. Use caution, as there will be energy stored in the torsion spring.
Raise the front of the machine so there is enough clearance to slide the deck underneath, and line up slots with the drag-link.
Slowly lower the machine over the drag links until the holes line up in the frame. Insert the pins and secure it with bolts (5/16 inch).
Raise the machine slightly until the block can be easily removed from underneath the drag-links.
Lower the machine until the chains can be attached with clevis pins and retainer clips. The machine my need to be started and the lift arms lowered to the lowest position so the chains will reach the deck.
After the deck is attached, slide the driveshaft over the gear box spline until the holes are aligned. Insert the roll-pins and tighten the two bolts on the driveshaft.
Start the machine and raise the deck high enough to remove the furniture dollies.
To adjust and verify the height of cut, consult the Owner's Manual.
Maintenance Service Interval | Maintenance Procedure |
---|---|
After the first 10 hours | |
Every 50 hours | |
Every 200 hours |
If you leave the key in the ignition switch, someone could accidently start the engine and seriously injure you or other bystanders.
Remove the key from the ignition before you do any maintenance.
Lubricate the machine every 50 hours. Grease more frequently when operating conditions are extremely dusty or sandy.
Grease Type: General-purpose grease
Maintenance Service Interval | Maintenance Procedure |
---|---|
Every 50 hours |
Disengage the PTO and engage the parking brake.
Shut off the engine, remove the key, and wait for all moving parts to stop before leaving the operating position.
Clean the grease fittings with a rag. Make sure to scrape any paint off the front of the fitting(s).
Connect a grease gun to the fitting. Pump grease into the fittings until grease begins to ooze out of the bearings.
Wipe up any excess grease.
Grease the locations indicated in Figure 15.
Figure 15
- Grease locations
Grease the PTO shaft (Figure 16).
Figure 16
- Gearbox
- PTO shaft end yoke
Disconnect the battery before repairing the machine. Disconnect the negative terminal first and the positive last. Connect the positive terminal first and the negative last.
Charge the battery in an open, well-ventilated area, away from sparks and flames. Unplug the charger before connecting or disconnecting the battery.
Wear protective clothing and use insulated tools.
Refer to the Operator's Manual supplied with the cab for instructions on fuses.
If the machine has any electrical system issues, check the fuses. Grasp each fuse and remove them one at a time, checking to see if any are blown. If you need to replace a fuse, always use the same type and amperage rated fuse as the one you are replacing, otherwise you could damage the electrical system.
Toro 325d Groundsmaster Parts Manual Fuel Pump
Note: If a fuse blows frequently, you probably have a short in the electrical system and should have it serviced by a qualified service technician.
Toro 325d Engine
Thoroughly clean the machine and cab, paying special attention to the following areas:
PTO shaft assembly
All grease fittings and pivot points
Oil the spline on the PTO output shaft to prevent rusting
Check all fasteners for looseness and tighten them as necessary. Torque the 5 bolts securing the winter frame to the traction unit to 359 N⋅m (265 ft-lb).
Grease or oil all grease fittings and pivot points. Wipe off any excess lubricant.
Lightly sand and use touch up paint on painted areas that are scratched, chipped or rusted. Repair any dents in the metal body.
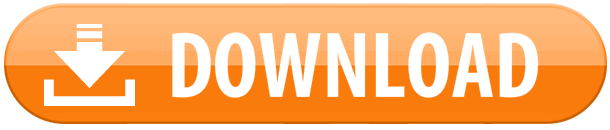